Bouncing sieve
Bouncing screen is a shutdown device with separation function designed for sorting inorganic particles in garbage after coarse crushing. This machine utilizes the characteristics of crushed waste materials to perform sorting operations based on the different densities of the materials when the waste reaches a certain particle size. The garbage bouncing sorting machine is designed with a bouncing function to bounce and separate inorganic particles or other hard particles while conveying materials. The separated particles move in the opposite direction to the conveyed material to achieve the purpose of sorting.
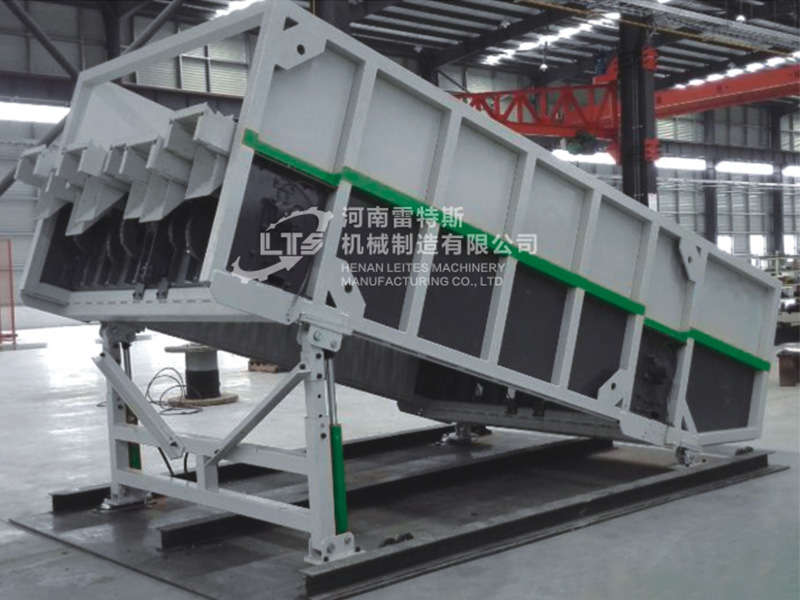
Dual-frequency screen
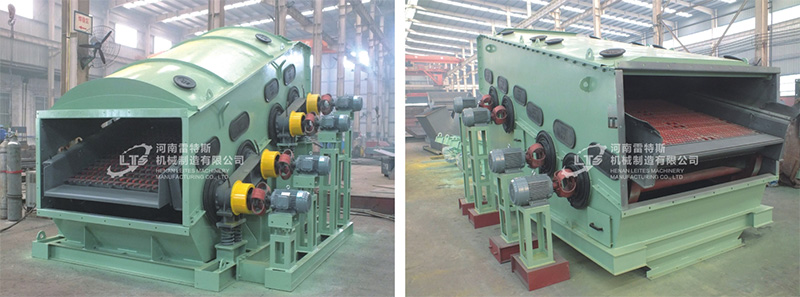
Multi frequency screening is mainly used in desulfurization systems for thermal power generation, screening systems for coal washing plants, solvent screening systems for steel enterprises (sintering, blast furnace, coking, raw material plants, etc. in the metallurgical industry), and sand and gravel aggregate systems in the construction industry. It adopts low amplitude, high frequency and other characteristics, and has advantages in screening small materials smaller than 5mm. It can also be extended to other industries and is mainly used for screening dry materials. The sieve plate mainly consists of bars, comb teeth, round steel welding, steel plate punching, etc. The re issuance of the sieve has changed the traditional structure of vibrating the sieve surface and the sieve box together. It adopts a motion mode of multiple independent sieve surfaces vibrating while the sieve box and frame do not vibrate. The multiple sieve surfaces vibrate independently from the inlet to the discharge end. Each section of the sieve plate has an independent vibration source and can vibrate independently, abandoning the traditional vibration mode of using the same vibration source, amplitude, and frequency for each section of the sieve plate. According to the particle size distribution of the materials on site, the size of the material quantity, the amplitude and frequency of each screening surface can be adjusted accordingly to achieve a better combination of processing capacity and screening efficiency. By adopting this structural approach, there are fewer moving parts and reduced vibration mass, so the unique structural design can reduce power compared to traditional screens. Since the vibrating screen box does not participate in vibration, it is easier to achieve a fully enclosed structure, which prevents dust from leaking out and meets higher environmental requirements.
Garbage sorting Site
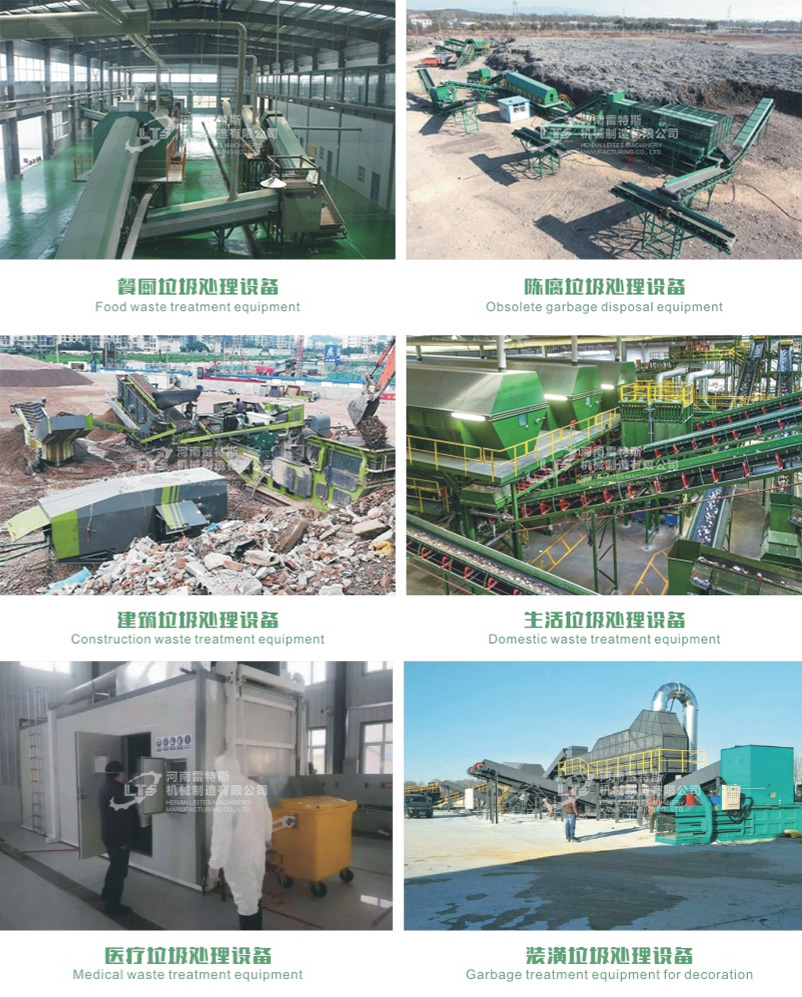