What is a crusher?
Before we discover all the different types of crushers – we need to know what a crusher is and what it is used for. A crusher is a machine that reduces large rocks into smaller rocks, gravel, or rock dust. Crushers are mainly used in the mining and construction industries, where they are used to break down very large rocks and boulders into smaller pieces. Crushers are also commonly used for jobs like breaking up asphalt for roadwork or demolition projects. Crusher machines come in a wide variety of sizes and capacities, from small jaw crushers that cost the same as a new truck to extra large cone crushers that cost millions of dollars. With all this choice you’ll want to make sure that the one you choose has the power and capabilities necessary for your specific project. In most cases, having a crusher at your disposal can save a significant amount of time and labor since you won’t have to do as much manually crushing materials yourself. This makes them an invaluable asset for anyone who may need to crush materials quickly and efficiently.
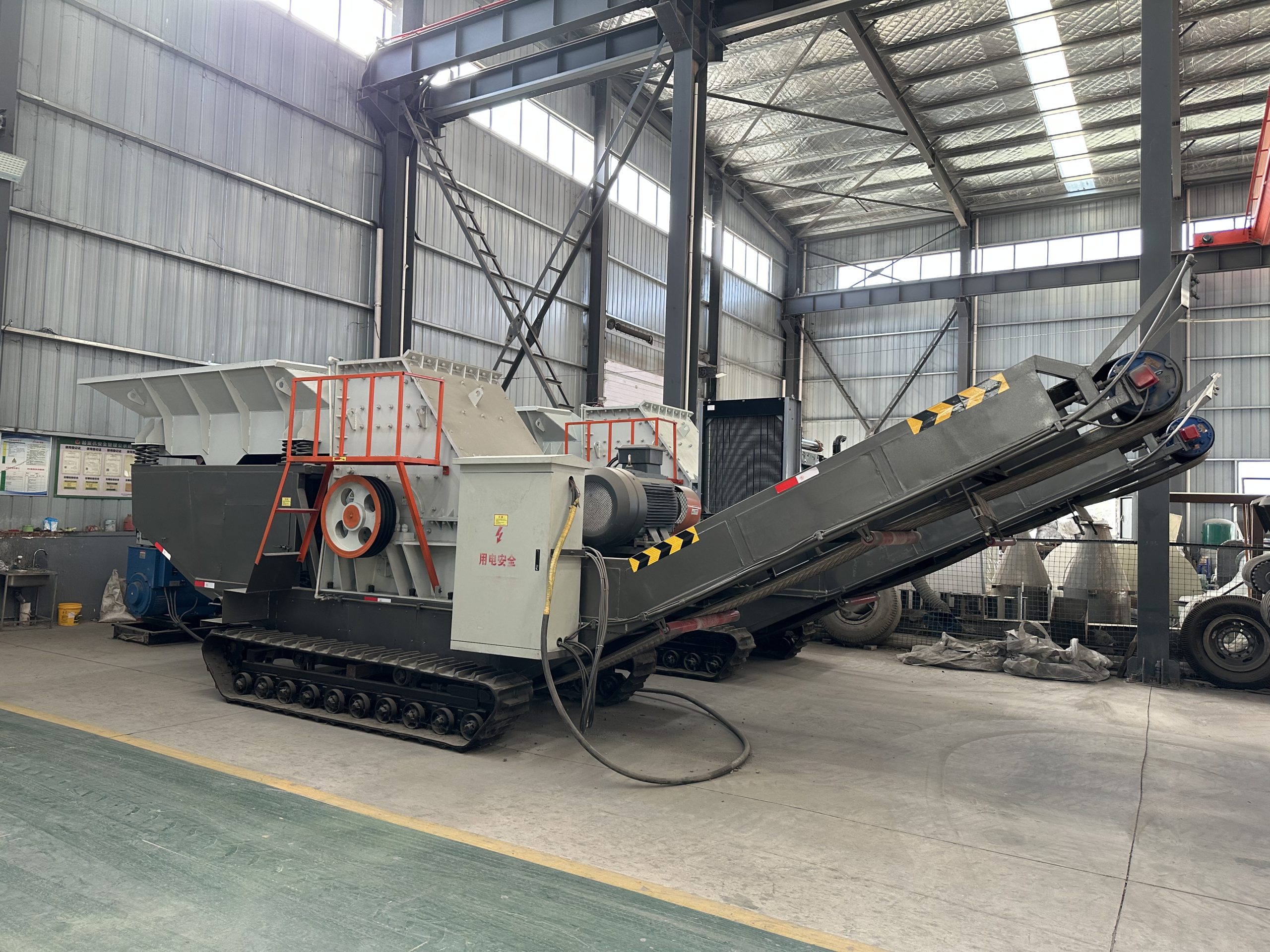
Brief history of crushers
The first United States patent for a rock crushing machine was in 1830. Its key technology was the drop hammer concept, found in the well-known stamp mill, which would be repeatedly linked to the golden age of mining. Ten years later, another U.S. patent was issued to an impact crusher. The primitive impact crusher was made up of a wooden box, cylindrical wooden drum, with iron hammers fastened to it. While both of these patents were granted, neither creator ever marketed their inventions.
Eli Whitney Blake invented, patented, and sold the first actual rock crusher in 1858, it was known as the Blake Jaw Crusher. Blake’s crusher was so influential that today’s models are still compared to his original designs. This is because the Blake Jaw Crusher integrated a key mechanical principle – the toggle linkage – a concept students of mechanics are familiar with.
In 1881, Philetus W. Gates received a U.S. patent for his device featuring the basic ideas of today’s gyratory crushers. In 1883 Mr. Blake challenged Mr. Gates to crush 9 cubic yards of stone in a contest to see which crusher would finish the job faster. The Gates crusher completed the task 40 minutes sooner!
The Gates’ gyratory crushers were preferred by the mining industry for almost two decades until the turn of the century, circa 1910, when Blake’s jaw crushers saw a resurgence in popularity. The demand for large-mouthed jaw crushers skyrocketed as the industry began to understand their potential as primary crushers in rock quarries. Through Thomas A. Edison’s research and development, giant machines were innovated and placed around the United States. Smaller-sized jaw crushers were also developed as secondary and tertiary crushers.
Edison’s studies within the field of mining and crushing left a legacy that forever improved how large rocks and materials are reduced.
Basic ways to reduce material size
Crushing is the process of reducing or breaking down larger-sized material into smaller-sized material. There are four basic ways to crush.
Impact: Instant collisions of large objects against one another with material placed between. Both objects can be in motion or one can be still while the other strikes against it. There are two main types of impact reduction, gravity and dynamic.
Attrition: Rubbing the material between two solid surfaces. This is an appropriate method when reducing less abrasive materials because it consumes less power during the process. Robust materials would not be as efficient.
Shear: Typically combined with other reduction methods, shearing uses a trimming method and is used when a coarse outcome is wanted. This reduction method is often seen in primary crushing.
Compression: A key mechanical element of jaw crushers, compression reduces materials between two surfaces. Great for very hard, abrasive materials that do not fit attrition crushers. Compression is unsuitable for anything tacky or gummy.
Choosing the correct type of crushing method is unique to both the type of material you are breaking down and desired product. Next, you must decide which type of crusher is best suited for the job. Keeping energy usage and efficiency in mind is always a top consideration. Using the wrong type of crusher can lead to costly delays and consume more power than expected during the process.
What are the different kinds of crushers?
There are lots of different kinds of crushers from jaw crushers to impactors and cone crushers. Crushing is an versatile process and the kind of crusher you need depends on the ‘stage’ of crushing. The three main stages of crushing are primary, secondary, and tertiary – all of which have their own unique benefits. Primary crushing involves using a large object as the initial force to break down very large and hard rocks and boulders into smaller pieces before they move onto the secondary stage. Secondary crushing breaks down materials even further before they go to tertiary level, which makes an even finer product that can then be used in various industrial projects. Each type of crusher for each specific crushing stage is explained in greater detail below.
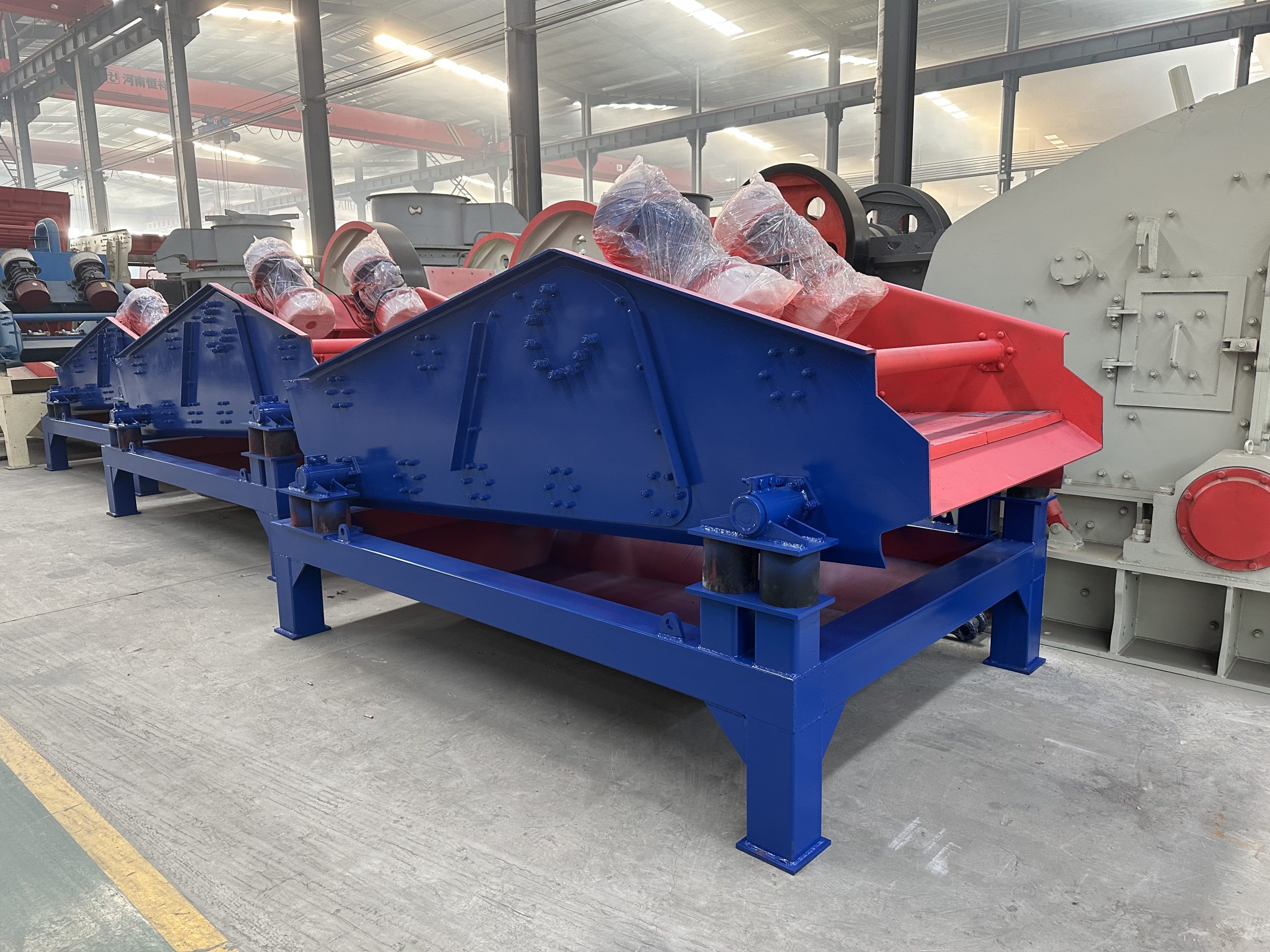