Project Background
A North China steel plant generates 800,000 tons of steel slag annually. Traditional disposal—landfilling or low-value sales—wastes land, pollutes soil, and ignores recoverable iron (15-20%) and aggregates. In 2023, Xuzhou Heavy Industry customized a crawler steel slag crushing and screening system to achieve “zero landfill” and resource utilization, aligning with China’s “Zero-Waste City” initiative.
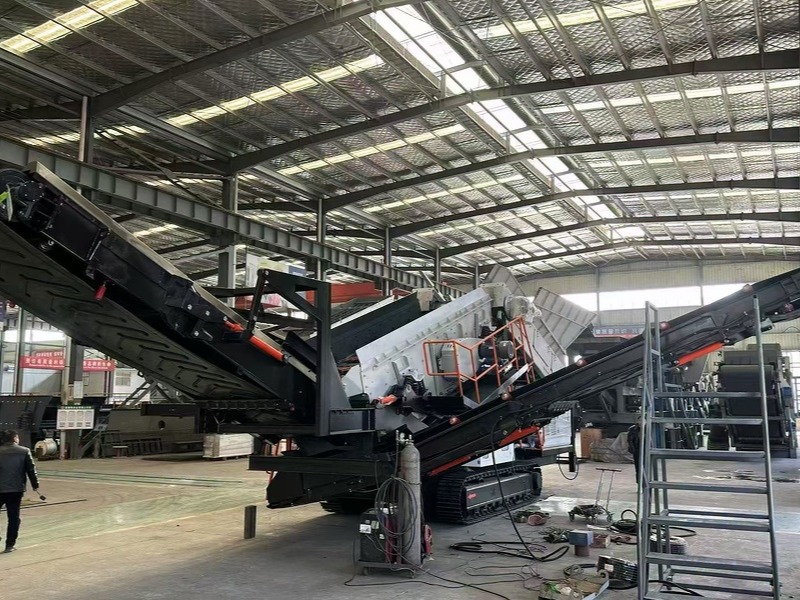
Challenges & Solutions
- High-Hardness, Metal-Rich Material Handling
- Challenge: Steel slag (Mohs 7-8) contains free calcium oxide (risking expansion) and scrap steel (0-500mm), causing rapid wear and jamming in traditional equipment.
- Solution:
–Dual-Stage Crushing: Primary jaw crusher (XZ950) reduces size to ≤150mm, secondary hydraulic cone crusher (XZ300S) to ≤30mm. Chromium-molybdenum alloy liners increase wear life by 40%.
–Magnetic Separation: High-intensity magnetic rollers (≥1.2T) recover 98% of scrap steel during screening, worth $3.3 million annually through re-smelting.
- Residual Heat & Dust Pollution
- Challenge: Slag 卸料温度 (discharge temperature) 200-300℃ requires 48-hour cooling, and dust exceeds national standards by 300% (GBZ2.1-2019 ≤8mg/m³).
- Solution:
–Waste Heat Recovery: Water-cooled crushing chamber shells reuse slag heat for factory heating, saving $70,000 in steam costs annually while preventing overheating.
–Closed-Loop Dust Control: Sealed crushing/screening with bag filters + cyclone separators reduces emissions to 3mg/m³, 62.5% below standards.
- Complex Plant Environment Adaptation
- Challenge: Narrow factory roads (≤6m width) and frequent slag yard relocations demand mobile flexibility.
- Solution:
–Compact Modular Design: 12m length, 3.2m width for narrow-road navigation; track ground pressure ≤0.5MPa suits factory pavement.
–Remote Control: 500m wireless operation allows safe operation away from high-temperature/dust zones.
Technical Highlights
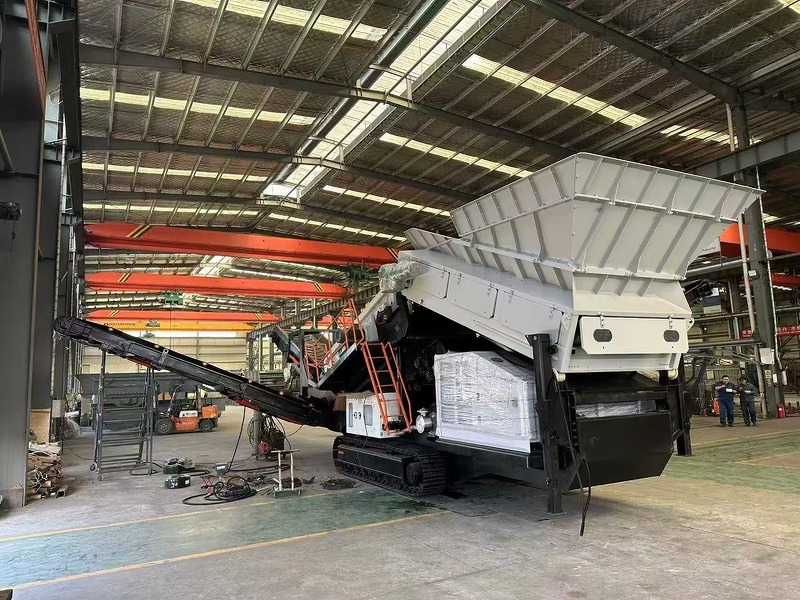
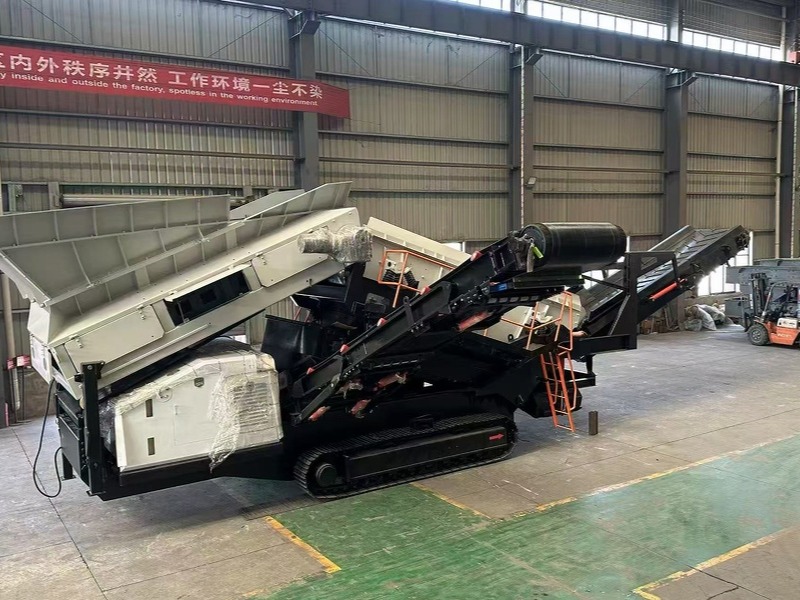
- Core Equipment
–Crawler Jaw Crusher: 950×600mm feed opening, 180 tons/hour capacity, with hydraulic overload protection to auto-release metal blocks, minimizing downtime.
–Smart Screening: Three-layer vibratory screen (5mm/15mm/30mm) uses AI vision to analyze aggregate size in real time, auto-adjusting crusher discharge for ≥95% 0-30mm output. - Digital Management Platform
–IoT Monitoring: 20+ real-time sensors track oil temperature, vibration, energy, etc., with 92% fault diagnosis accuracy via automatic alerts.
–Cloud System: Integrates with the plant’s ERP to sync slag processed, scrap recovered, and costs, enabling dynamic production planning.
Implementation Results
- Resource Recovery & Economics
–Processing Capacity: 750,000 tons/year slag treated, utilization up from 30% to 95%, producing 500,000 tons recycled aggregates and 120,000 tons scrap steel ($3.3M value).
–Cost Savings: $1.1M/year landfill savings, 65% lower transportation costs, 22-month payback period. - Environmental & Social Impact
–Emissions Reductions: 150 mu (10 hectares) land saved, 87.5% dust reduction, awarded “Industrial Waste Recycling Model Project” by MEE.
–Industry Drive: Established a full “slag crushing-magnetic separation-screening-recycled aggregate” chain, reducing local natural sand mining by 300,000 tons/year. - Intelligent Upgrades
–Maintenance Efficiency: 70% fewer manual inspections, 85% equipment utilization, 55% less downtime.
–Data-Driven Optimization: Energy consumption per ton dropped from 0.8kWh to 0.6kWh, saving 150,000 kWh annually.
Conclusion
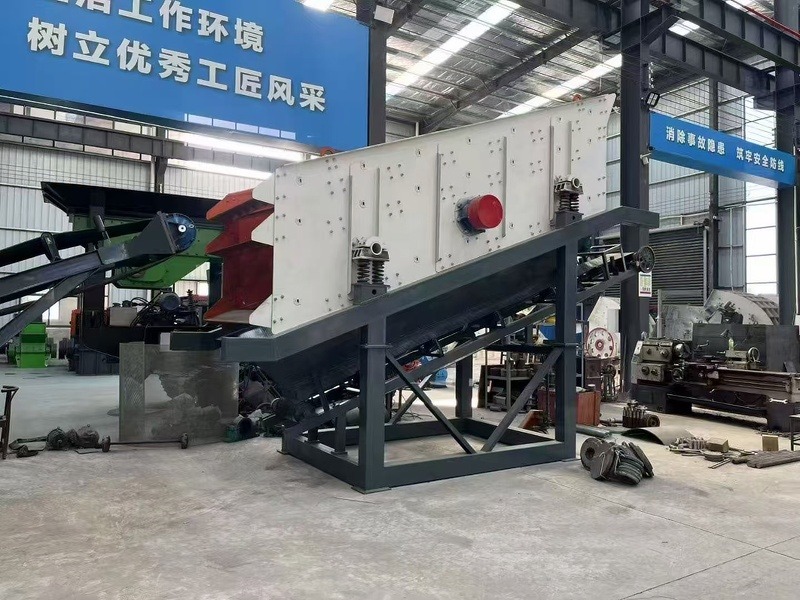

The Chinese steel slag project highlights crawler crushers’ unique value in industrial waste: through wear-resistant technology, magnetic integration, and intelligence, they solve hard-material challenges while creating a “resource recovery-environmental protection-economy” cycle. As global steel production and circular economy policies grow, such solutions will dominate slag/slag-like waste treatment, advancing carbon neutrality and sustainable development.