For a complete crushing production line, in order to produce sand and gravel aggregates of right size, the raw materials generally need to go through three to four crushing and shaping processes. In different crushing stages, different stone crusher is required. Using the different characteristics of the equipment, the raw materials can be crushed to the required particle size.
There are many types of common crushers on the market, such as jaw crushers, cone crushers, impact crushers, vertical shaft impact crushers, etc. So in different crushing stages, how should customers choose a suitable crusher?
Primary crushing (Coarse crushing)
Primary crushing, also known as coarse crushing, is mainly used for the initial crushing of large pieces of material, and the particle size of the crushed materials is generally large. In the primary crushing stage, the feed size is about 500 to 1500 mm, and the output size is generally 100 to 350 mm.
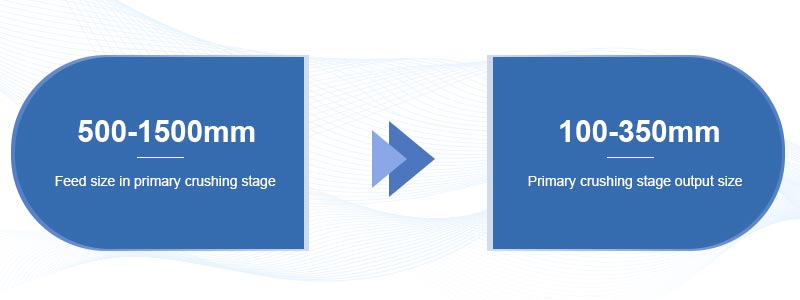
Crushers commonly used in the primary crushing stage
The commonly used crushers in the primary crushing stage are jaw crushers and gyratory crushers.
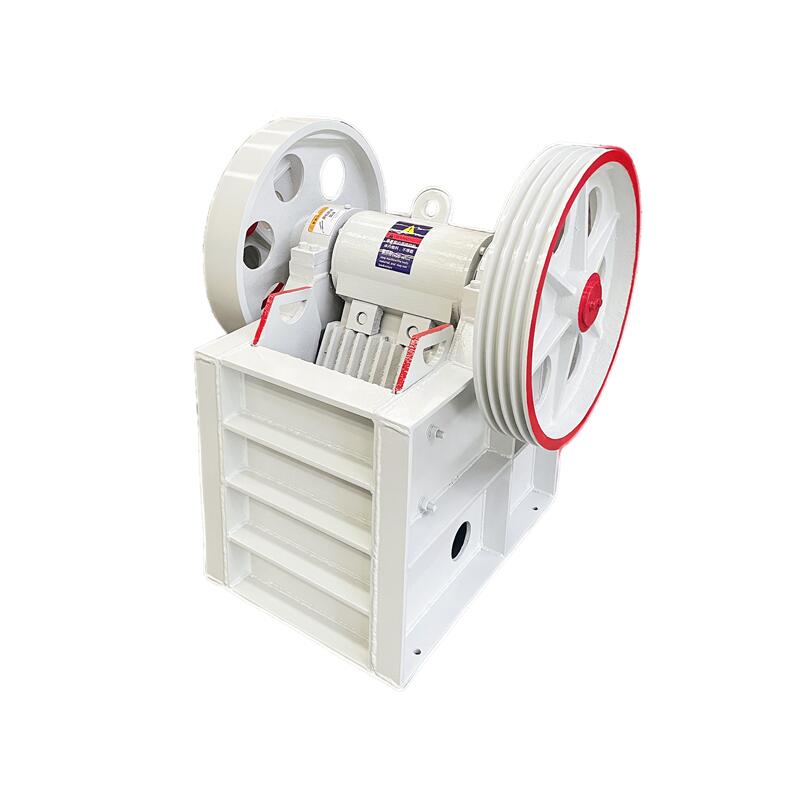
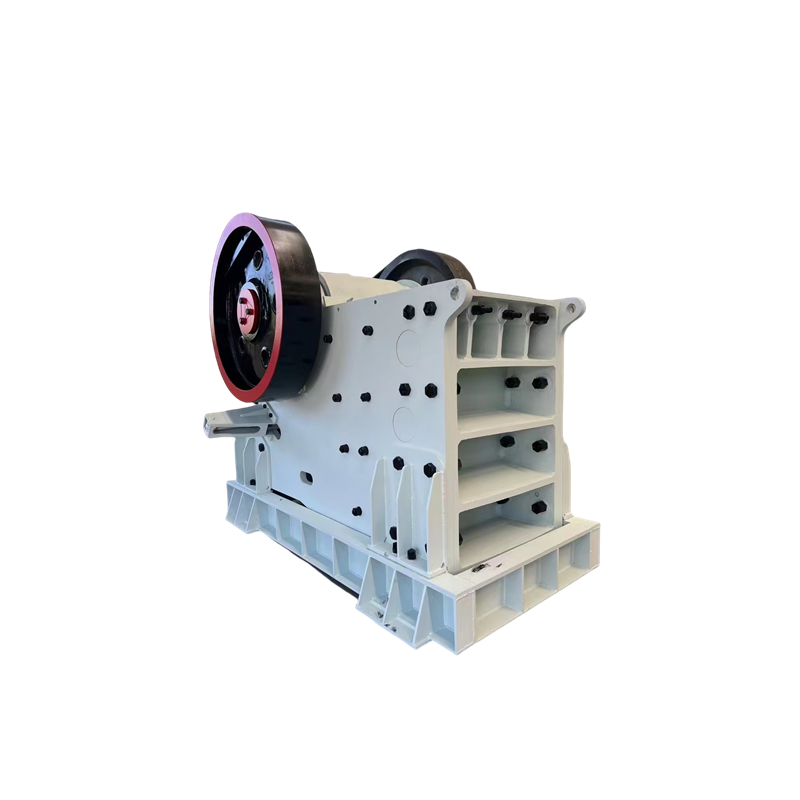
The jaw crusher is an earlier crushing equipment. Because of its simple structure, reliable operation, easy maintenance and low cost, jaw crushers have been widely used in metallurgy, chemical industry, building materials, electric power and other fields.
The jaw crusher mainly realizes the crushing of materials through the mutual extrusion of the jaw plates, and is the first choice for crushing hard materials such as granite.
Gyratory crusher
Gyratory crushers are also known as vertical compound crushers. Because of its high crushing efficiency, large feeding size, simple production process and low maintenance cost, the gyratory crusher has always been an ideal equipment for coarse crushing of relatively hard materials in large mines and other fields.
Seondary and tertiary crushing (Medium and fine crusher)
The secondary and tertiary crushing is also called medium and fine crushing, which mainly crushes the materials after the primary crushing. If you require a larger output particle size, then secondary crushing can meet the requirements; if you require a smaller output particle size, then you need to perform tertiary crushing.
In the secondary crushing stage, the material is crushed from 350 to 100mm to 100 to 40mm.
In the tertiary crushing stage, the material is crushed from 100 to 40mm to 30 to 10mm.
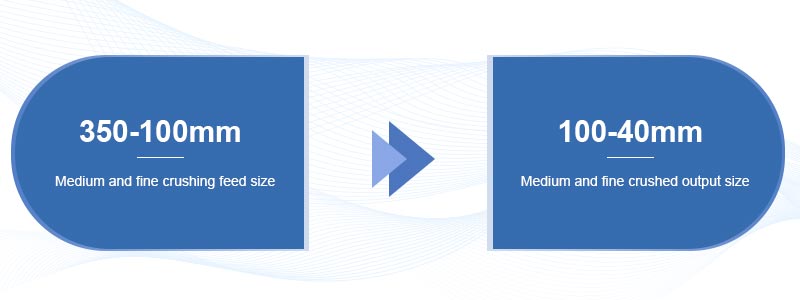
Crushers commonly used for medium and fine crushing
The most commonly used crushers in medium and fine crushing are cone crushers and impact crushers. In recent years, due to the appearance of fine jaw crusher, its lower cost has also been welcomed by some customers.

The cone crusher is mainly suitable for crushing various rocks and ores with medium and above medium hardness, such as granite and pebbles.
There are five common types of cone crushers, including spring cone crushers, Symons cone crushers, compound cone crushers, single-cylinder hydraulic cone crushers, and multi-cylinder hydraulic cone crushers. Customers can choose the appropriate cone crusher according to actual needs.
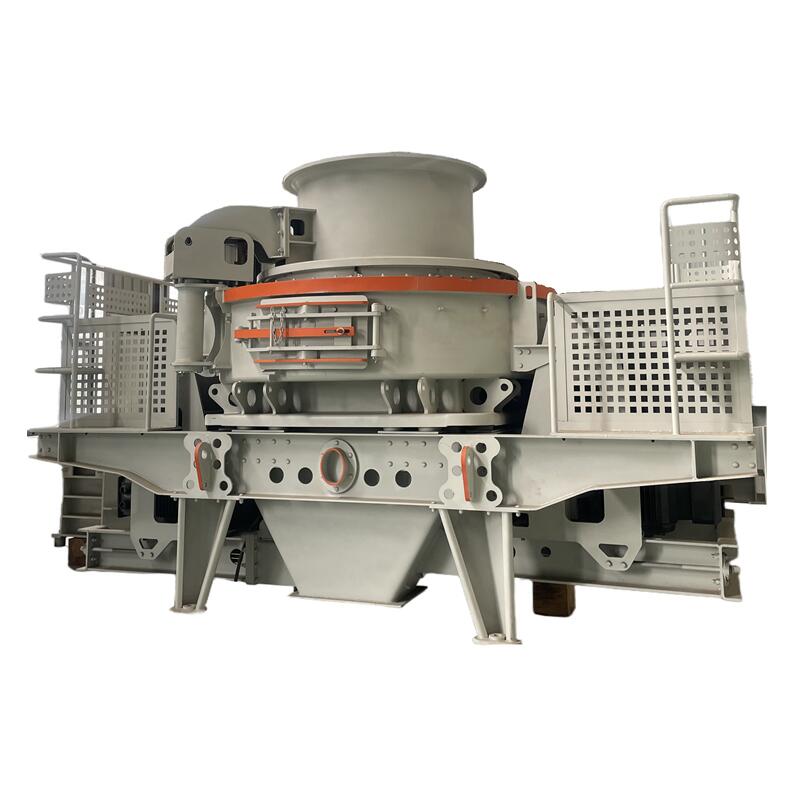
Impact crusher is a device that uses impact energy to crush materials. It is mainly used to crush brittle materials of medium hardness and below. The material crushed by impact crusher is mostly cubic in shape.
At the same time, it also has the characteristics of high production efficiency, large crushing ratio, compact structure, good product shape and strong impact resistance.
Sand making and shaping stage
If the size and grain shape of the produced material cannot meet your requirements, you can consider adding a sand making machine to crush and shape the material again. The equipment commonly used at this stage is a sand making machine.
Sand making machine (Vertical shaft impact crusher)
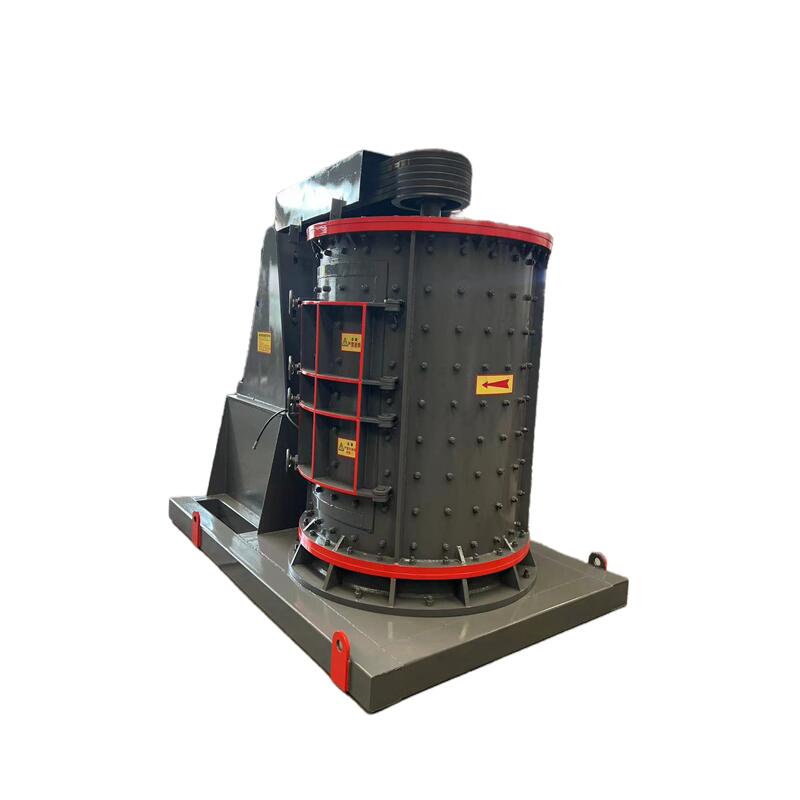
Sand making machine can also be called vertical shaft impact crusher. It is widely used in sand making and shaping of limestone, river pebbles, granite, ore tailings and other materials. It can provide high-quality sand and gravel aggregates for highways, high-rise buildings, municipal engineering, stone factories, hydropower dam projects, concrete mixing plants, etc.
Generally speaking, the feeding size of sand making machine is less than 40mm and the discharging size is 0 to 10mm.
In recent years, because of the protection of river sand resources and the increase of demand for sand and gravel aggregate, more and more customers want to invest in a suitable sand making production line. So what are the advantages of sand making machine?
Advantages of sand making machine
The finished sand has good grain shape. The grain shape of the sand produced by vertical shaft impact crusher is excellent, mostly cubic in shape, with low content of needle-shaped materials. Moreover, its fineness modulus can be adjusted at will.
Unique design, easy maintenance. The hydraulic cover opening device makes the internal inspection and maintenance of the crushing chamber convenient, saving time and effort.
Thin oil lubrication reduces labor intensity. The vertical shaft impact crusher is equipped with a thin oil lubrication station, which automatically stops when there is no oil flow and oil pressure, ensuring that the bearing lubrication is always in the best state and prolonging the service life of the equipment. It also reduces the labor intensity of workers.
Multiple feeding methods can be converted. It can realize the conversion between the two feeding methods of full center feeding and center feeding with cascading feeding. Moreover, it can also realize the conversion of “stone hitting stone” and “stone hitting iron”, one machine with multiple functions, adapting to the requirements of different users.
Less pollution. The unique air circulation system greatly reduces the amount of external air exhaust, reduces dust pollution and reduces pollution to the surrounding environment.
Before investing in a satisfactory crushing production line, you need to comprehensively consider the hardness of the material, the feeding size and discharging size, the output, the investment cost, and the particle shape of the finished material. If you have any confusion, please feel free to consult us!