Small jobsite crushers offer a slew of benefits to the operator, including limiting the cost of hauling out construction and demolition debris from jobs and limiting the amount of new aggregate that needs to be brought in. The crushed material can also be sold or used for other landscaping or construction projects.
Jobsite crushers are also simple to operate and are easy to move from site to site, making them an attractive option for those who regularly find themselves paying to remove aggregate debris or to bring in new aggregate for jobs.
If you have a jobsite crusher or are ready to operate a jobsite crusher and want to ensure success, a little prep work goes a long way. Follow these tips for preparing the site, material and crusher for optimum and efficient operation.
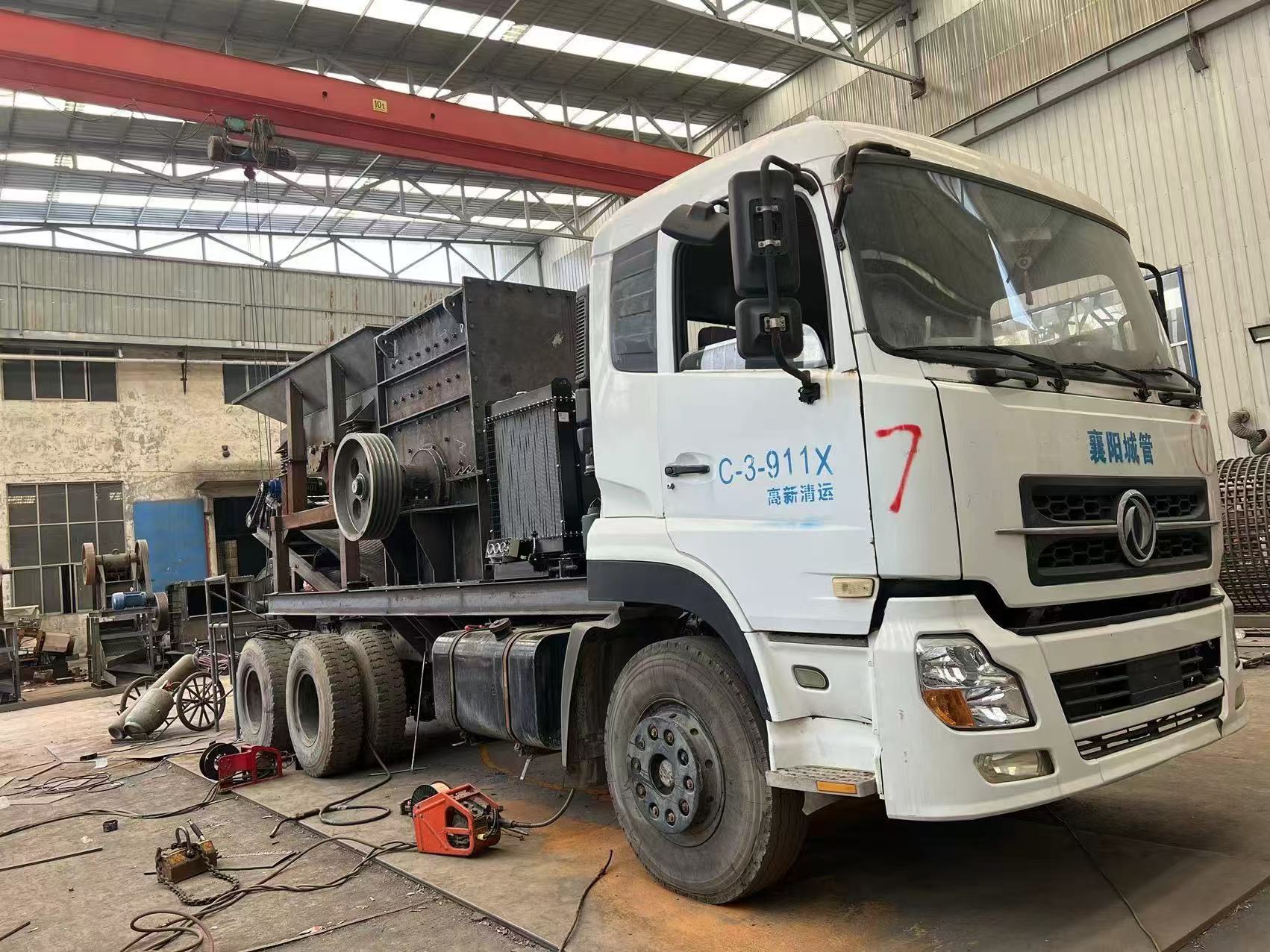
Ready the site
The first step for successful crusher operation is to prepare the site for crushing. While compact, mobile crushers are adept at fitting into small areas, such as urban developments, you still want to ensure you have enough room for the feed piles and material stockpiles, as well as for the crusher and material handling equipment to move freely.
Clear the area of any debris, vegetation or obstacles that may interfere with the operation of the crusher. If necessary, level the ground to provide a stable working surface for the crusher.
Pro tip: For most efficient crusher operation, it is best to feed the crusher from a slightly elevated position so that the loader operator can see into the crushing chamber. Consider building a level pad of material near the crusher from which the loader can feed.
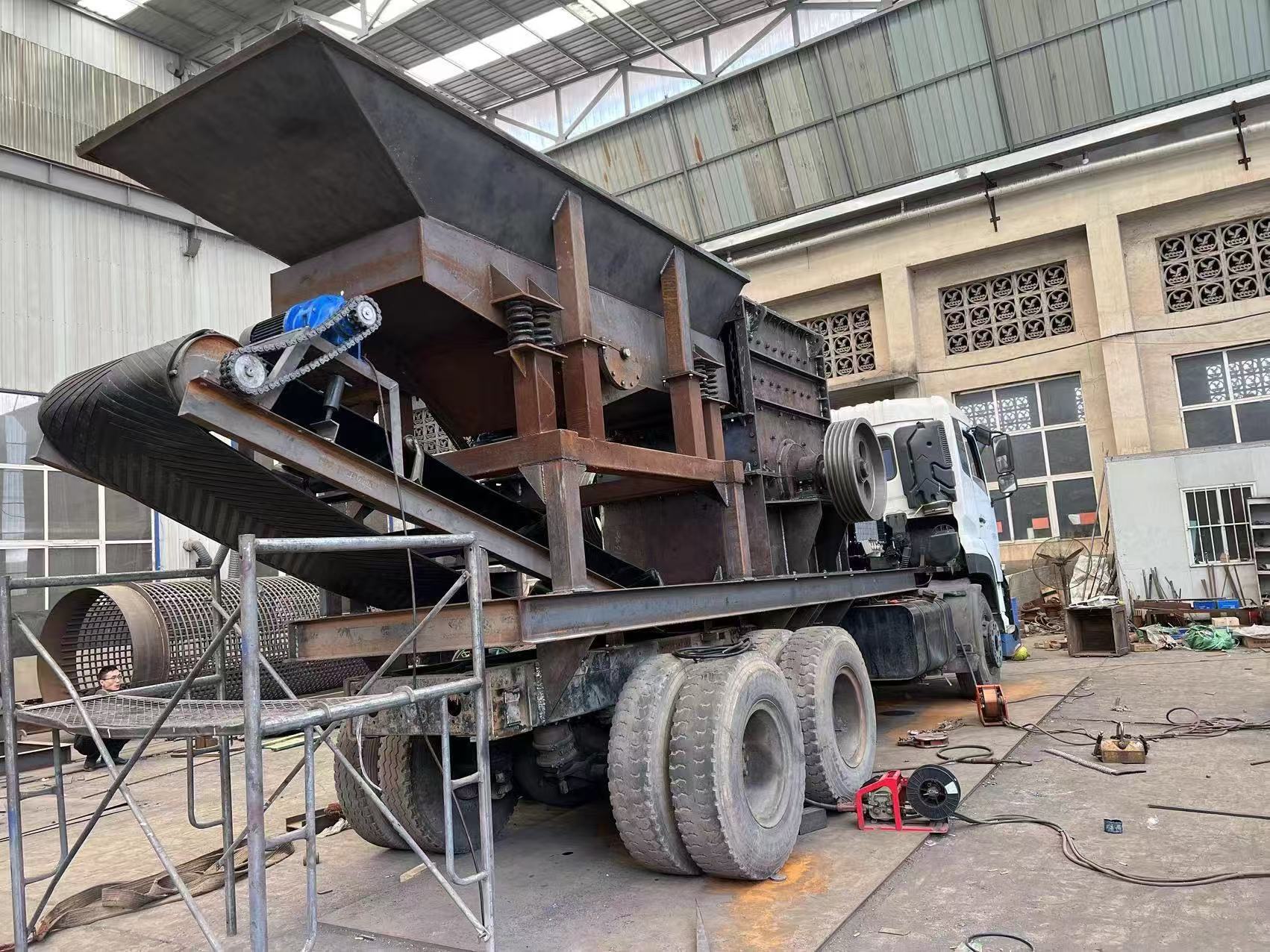
Sort and prepare the material
Inspect the material to be crushed before loading it into the crusher. Remove any contaminants or foreign objects, such as rebar or metal, that could damage the crusher or affect the quality of the crushed material. Properly manage and dispose of any waste materials not to be crushed according to local regulations and environmental guidelines.
Sort the feed material by size, type and quality. Depending on the size of the crusher, the material may be too large for the crusher to handle without some prior processing. Each crusher has a top size it can be fed, typically as large as 80% of the jaw opening. For example, the RC150 series jaw crushers, with crushing chambers measuring 26”x14”, can accept a single lump size as large as 21” x 11”; however, for more efficient crushing, the optimum lump size would be roughly the size of a basketball.
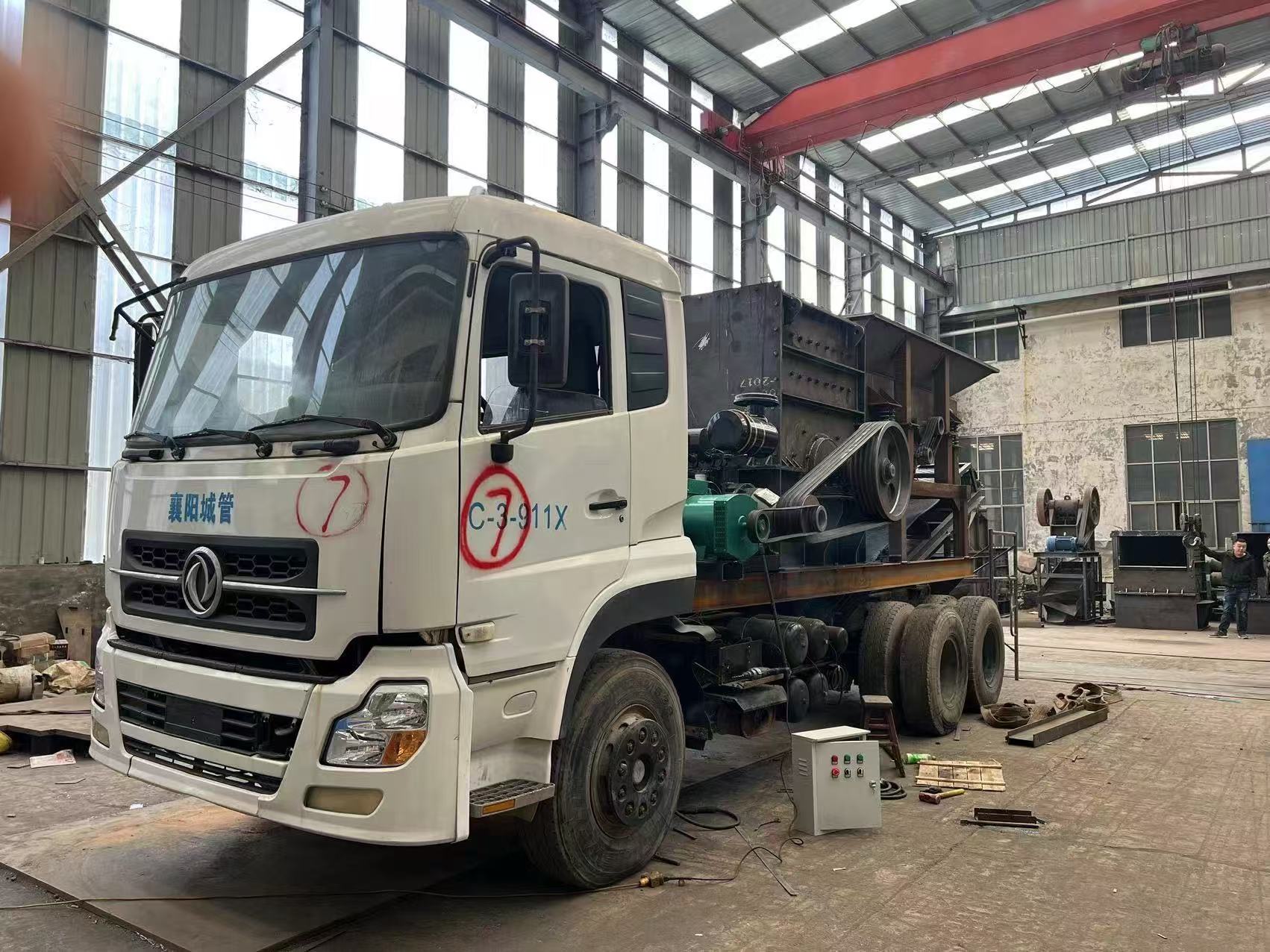
If your material is larger than the top size of the crusher allows, you’ll need to break down the material into smaller pieces before crushing to prevent chamber clogs or damage to the crusher, as well as to maximize the crusher’s efficiency. This can be accomplished with a hydraulic breaker or hammer attachment that is mounted to a skid-steer loader or excavator.
Likewise, if you have an excess of soils or fine material in the feed, remove it ahead of crushing for optimum crusher operation and best throughput.
Pro tip: Jobsite crushers can be adjusted to discharge a range of product sizes, so they can act as a primary and secondary crusher in one compact machine. To improve efficiency, consider crushing the material on the largest discharge setting first, and then feeding the crushed material back into the crusher a second time at a smaller setting to achieve a smaller product size.
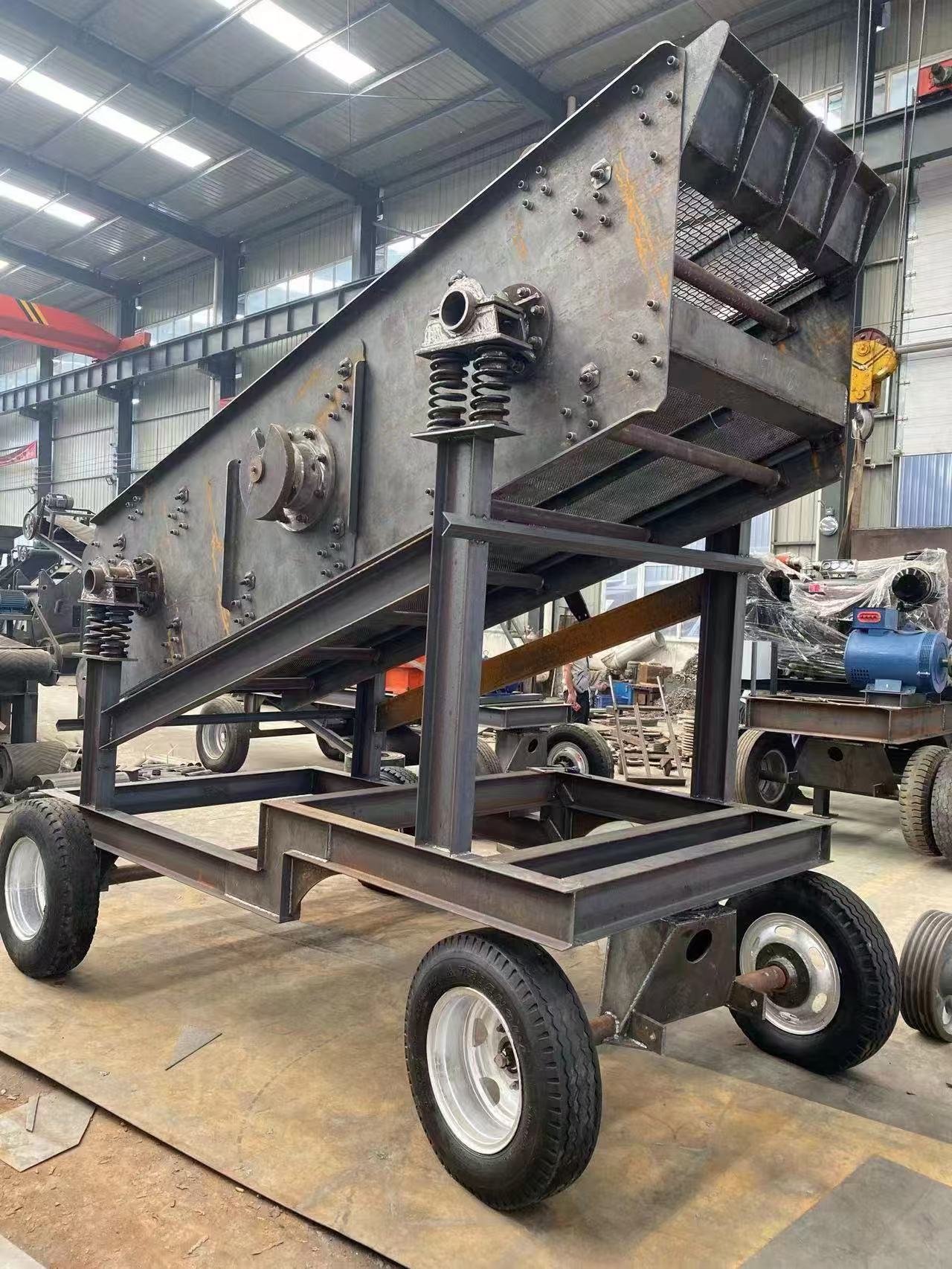
Crushing considerations
Before crushing, consider how you plan to feed the crusher. Most jobsite crushers can be fed with a mini excavator or skid-steer loader. If you don’t already have one of these in your equipment arsenal, consider renting one locally, looking into leasing opportunities or making the investment to buy one.
Position the crusher in a suitable location near material stockpiles but with enough room for the discharging product pile to form. Ensure the crusher is stable and level before putting material into it. Adjust the crusher settings to achieve the desired product size.
For best results, be sure to follow the manufacturer’s set-up and operation instructions, as well as any recommended guidance on feeding best practices. Regularly monitor the crusher to ensure it is performing as intended, and don’t forget about maintenance. Even if you are only renting the crusher for a few days or weeks, you may need to add grease or fuel daily, or you may need to adjust a misaligned conveyor belt. In all instances, it is best to be familiar with the manufacturer’s recommended maintenance schedule and practices.
Pro tip: Consider adding a jobsite screener to sort the crushed product into final sizes for stockpiling.
Safety first
Ensure all personnel involved in the crushing operation are trained in safe work practices and use appropriate personal protective equipment. Establish clear communication channels and safety procedures to minimize the risk of accidents or injuries. Keep unauthorized personnel away from the crusher during operation. Regularly inspect the area around the crusher for potential hazards and address any concerns promptly.
When operating a jobsite crusher, preparing the site and material ahead of time, as well as following the crusher’s instruction manual and all safety guidelines, will help ensure a smooth, trouble-free, uninterrupted crushing process and have you crushing like a pro in no time!