
The machine has changed the original structure of the grinding machine, integrating the body and chassis, and can be hung on the foundation plane at once during installation. The main bearing adopts double row self-aligning spherical roller bearings, which can reduce energy consumption by 30%. Changing from grid based forced discharge to overflow based controlled discharge can improve the grinding particle size and increase processing capacity by 15-20%.
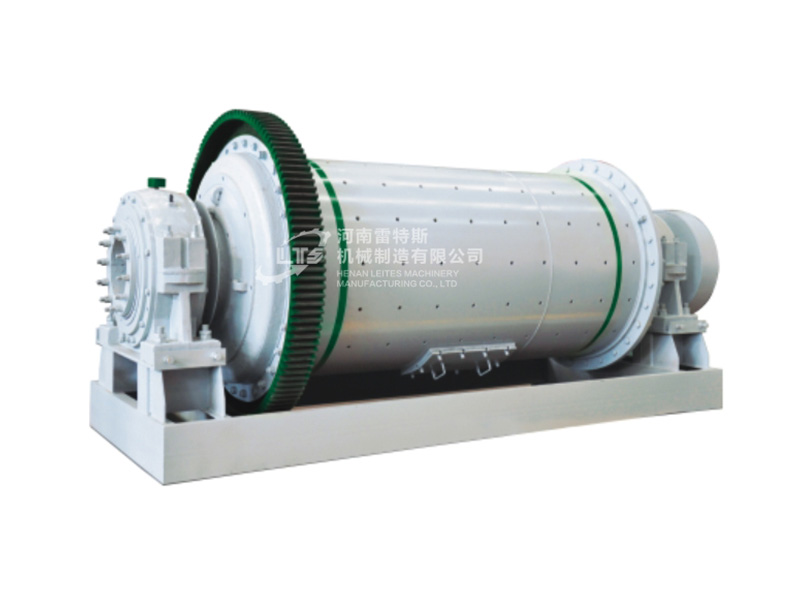
Working principle
Ball mill is composed of a horizontal cylinder, inlet and outlet hollow shaft and grinding parts, the cylinder is a long cylinder, the cylinder is equipped with a grinding body, the cylinder is made of steel plate, there is a steel lining plate and the cylinder is fixed, the grinding body is generally a steel ball, and is loaded into the cylinder according to different diameters and a certain proportion, the grinding body can also be used steel section. According to the particle size of the grinding material is selected, the material is loaded into the cylinder by the hollow shaft of the feed end of the ball mill. When the ball mill cylinder rotates, the grinding body is attached to the lining plate of the cylinder due to the action of inertia and centrifugal force, and the action of friction force, so that it is taken away by the cylinder. When it is brought to a certain height, it is thrown off due to its own gravity. The falling abrasive body acts like a projectile and shatters the material inside the cylinder.
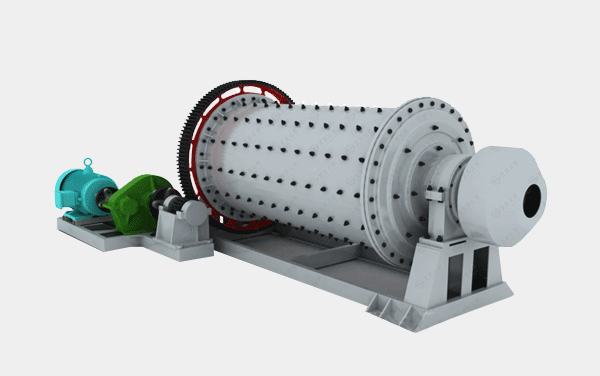