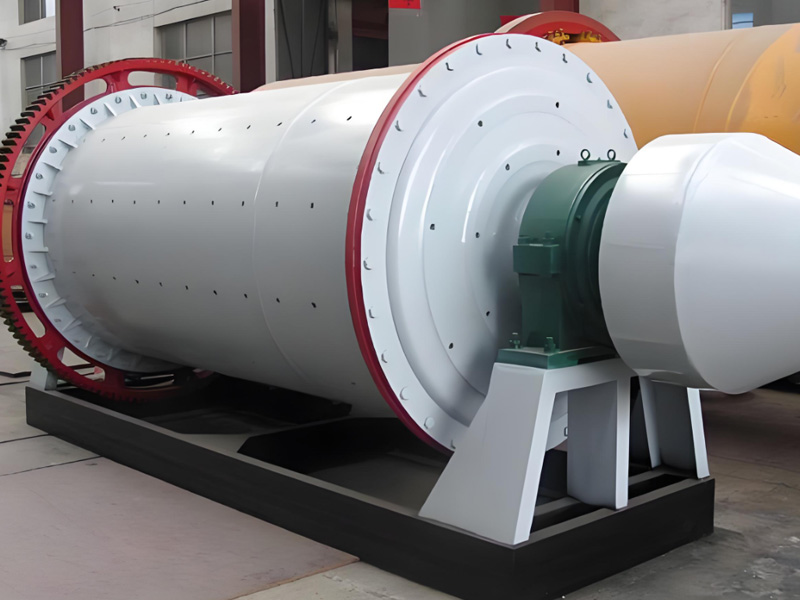
MB rod mills are widely used in industries such as metal and non-metal mines, water conservancy, and glass building materials to grind various ores, rocks, and artificial sand, which require uniform particle size and less material passing through the powder sand. The high-efficiency and energy-saving rod mills produced by our company are supported by rolling bearings instead of sliding bearings. Compared to sliding bearing support. Has energy savings of 10-20%. Under the same power conditions, it can increase production capacity by 10-20%.
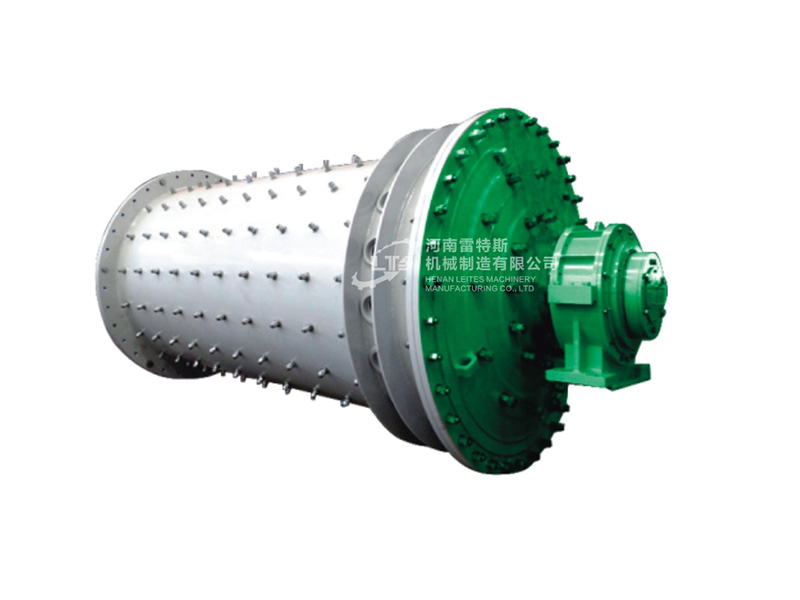
Working principle
Ball mill is composed of a horizontal cylinder, inlet and outlet hollow shaft and grinding parts, the cylinder is a long cylinder, the cylinder is equipped with a grinding body, the cylinder is made of steel plate, there is a steel lining plate and the cylinder is fixed, the grinding body is generally a steel ball, and is loaded into the cylinder according to different diameters and a certain proportion, the grinding body can also be used steel section. According to the particle size of the grinding material is selected, the material is loaded into the cylinder by the hollow shaft of the feed end of the ball mill. When the ball mill cylinder rotates, the grinding body is attached to the lining plate of the cylinder due to the action of inertia and centrifugal force, and the action of friction force, so that it is taken away by the cylinder. When it is brought to a certain height, it is thrown off due to its own gravity. The falling abrasive body acts like a projectile and shatters the material inside the cylinder.
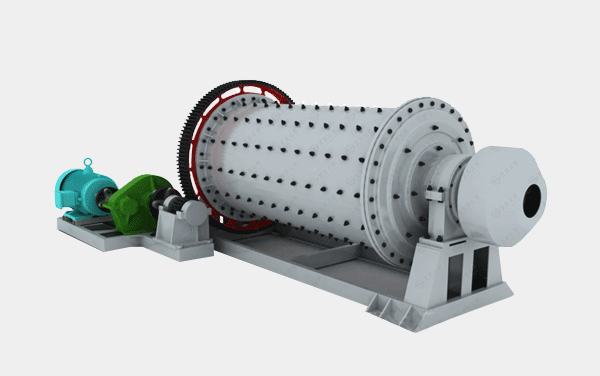