1. Working Principle
Hammer crusher: It is mainly composed of the machine body, transmission device, rotor, etc. And the transmission device includes a triangular belt, a winding motor, and a pulley; the rotor with a hammerhead is the component of the hammer crusher, and its surface has a layer of wear-resistant material to avoid excessive wear of the rotor.
Usually the rock ore is crushed under the action of a high-speed rotating hammerhead, and then the rock ore rebounded for further breaking on the counterattack board at a high-speed impact. Rock ore crushed multiple times during the whole process.
impact crusher: it is mainly composed of a body frame, transmission mechanisms, impact boards, and rotor. The body frame divided into two parts: upper and lower parts, and it uses the bolts to connect; The impact plate suspended inside the crushing chamber; The plate hammer on the rotor is its main spare part.
The material first hit the hammerhead,which is rotating and countered on the impact plate at a high -speed, so the broken material was thrown to the impact plate at the other end of the crushing chamber at high speed along the tangent direction, which is break again. We got fine size material by repeating like this.

2. Appearance, Applicable Material, And Discharge Size
- Appearance. There are two types of hammer crushers, namely small hammer crushers and heavy hammer crushers. The heavy hammer crusher is similar to the impact crusher, The front of them is similar, and the difference at the back of them is obvious. The back of the hammer crusher is a smooth arc, while the back of the impact crusher is angular.
- Applicable Material. The hammer crusher is suitable for crushing medium hardness stones with less than 200MPA. The impact crusher is suitable for handling brittle materials and has a compressive strength of no more than 350 MPa. Such as granite, limestone, concrete, etc.
- Discharge Size. The feeding size of the hammer crusher is 600-1800mm, and the output size is under 25mm. The impact crusher feeding size is no more than 500mm.
3. Maintenance And Damage Degree Of Spare Parts
Maintenance: There are a few plate hammers installed on the rotor of the impact crusher,which is convenient to do maintenance; The hammer crusher broken hammers can reach dozens at most, and replacement is time-consuming and labor-intensive. Moreover, the shape and size of the plate hammer and hammer head are also different, it makes some difficulty while changing spare parts.
Damage Degree Of Spare Parts: The wear of the plate hammer of the impact crusher only occurs on the side facing the material. When the rotor speed is running normally, the feeding material will fall to the striking surface of the plate hammer, and there is less wear on the back and side of the plate hammer. Even the wear on the side facing the material is less, and the metal utilization rate can be as high as 45% – 48%. The wear of the hammerhead of the hammer crusher occurs at the top, front, back, and side. Compared to the hammer plate, the wear of the hammerhead is more serious, and the metal utilization rate of the hammerhead is only about 25%.
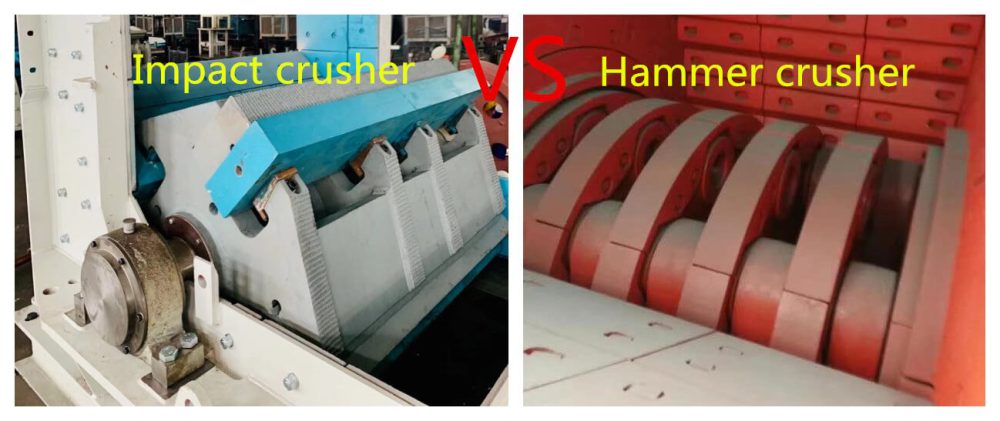
4. Advantages
Advantage of hammer crusher
(1) The crushing ratio is fast, and the product can be crushed and shaped for one time. The product has good particle size and less excessive powder;
(2) Hammer crusher integrates the functions of coarse crushing and shaping without a screen plate which will reduce plugging;
(3) a single heavy hammer crusher capacity can reach 3000tph, which is very popular in large sand-making plants.
Advantages of impact crusher :
(1) With strong adaptability, it is suitable for crushing hard, soft, brittle, and tough materials with high water content. The finished products are most cubic with uniform particle sizes.
(2) The crushing ratio is big, generally 20-50, and the bigger one reaches 150, which can complete the medium and fine crushing operations for one time, and the production process is greatly simplified.
Usually, the hammer crusher and the impact crusher considered as a second stone-crushing machine in a sand-crushing plant. For a complete stone or sand crushing plant, the first auxiliary equipment is a vibrating feeder, and the jaw crusher is the primary crushing machine, the second crushing machine can be an impact crusher, hammer crusher, cone crusher, etc. If it is a big capacity sand crushing line, there will need a third sand-making machine, a VSI sand making machine, After it, there are vibrating screens to screen the coarse sand and fine sand. and the whole stone or sand-making plant are connected by several belt conveyor.
After analyzing the hammer crusher and impact crusher in many ways, we believe you already have some ideas about their production performance and advantage. If you are still confusing which machine to choose, make choices based on the material type, output size, and capacity requirement. Contact our professional engineers for a consultation! Get the factory prices!